Steel Structure Intelligent Production Line: Breaking the Shackles of Capacity Constraints, Setting a New Benchmark for Industry Efficiency
Release Date:
2025-04-24 13:37
Source:
Intelligent Production Line Solution for Steel Structures
Lean Intelligent Manufacturing Solution Provider
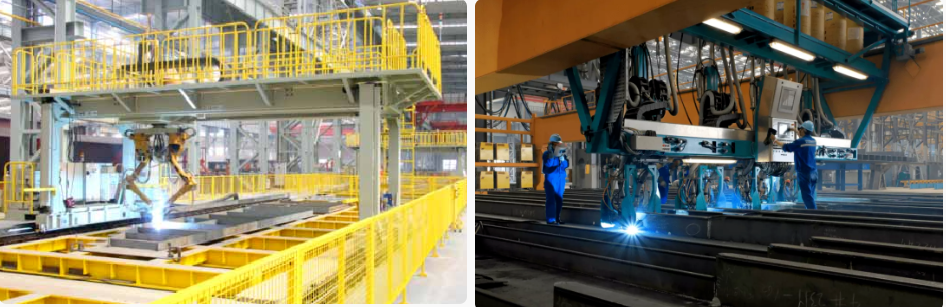
In the construction and engineering sectors, steel structures are widely adopted for their high strength, lightweight properties, and rapid construction. However, traditional steel structure production faces challenges such as low manual labor efficiency and recruitment difficulties. NAEC’s Intelligent Steel Structure Production Line Solution empowers traditional steel fabrication enterprises to overcome core challenges like "labor shortages + low efficiency," significantly boosting production capacity.
Steel structures come in various forms, including those made from steel plates, structural steel, steel pipes, steel cables, and other materials connected by welding, riveting, bolts, etc., forming heavy-duty, high-rise, large-span, or lightweight structures. Based on application scenarios, they can be categorized into:
■ Onshore and offshore industrial Engineering Steel Structures;
■ Architectural steel structures (mainly composed of structural steel and steel plates, forming beams, columns, and trusses);
■ Bridge and shipbuilding steel structures (large bridges and ships require high wind resistance and load-bearing capacity. High-strength steel is commonly used in design, along with corrosion-resistant steel for marine environments and low-alloy steel to reduce welding costs and complexity);
■ Metal structures for machinery manufacturing ((cranes, tunnel boring machines, etc.)
Intelligent Steel Structure Production
Breaking Through Traditional Bottlenecks, Unleashing Production Capacity
NAEC is committed to solving the problems caused by traditional manual operations that constrain enterprise capacity, such as the recruitment and retention difficulties of specialized workers in welding and painting, as well as low production efficiency. By applying intelligent manufacturing technologies, the demand for specialized labor is reduced, while the proportion of skilled technicians is increased. This approach can improve production capacity by 1.5 to 3 times.

Relying on Core Intelligent Equipment & Technologies
1.High-Precision Cutting Equipment: High-precision laser cutting machines, fully automatic CNC pipe intersecting line cutting machines, high-precision plasma cutting machines, and 3D stereoscopic plasma precision cutting trolleys. These devices achieve cutting accuracy within ±0.5mm, ensuring high-quality processing and rapid output of components in preliminary processes.
2.Automated Machining Equipment: Automated presses, automatic feeding CNC bending machines, CNC flat drilling machines, radial drilling machines, and plate rolling machines. These automated machining tools ensure high-precision product processing and efficient output, supporting seamless intelligent logistics integration.
3.Welding Robots & Advanced Technologies: Welding robots equipped with fine recognition technology, high-precision 3D modeling algorithms,3D modeling, point cloud registration, and 3D correction algorithms. Advanced technologies such as structured light high-precision imaging and complex scene compensation optimization enable flexible task monitoring and scheduling, supporting a wide range of part types.
Through these intelligent devices, combined with software and hardware, dynamic management of the production process, predictive maintenance execution, and process improvement are achieved, enabling intelligent management and decision-making. This ensures the smooth implementation of intelligent steel structure production projects.
Robotic Workstations: Achieving High-Efficiency Production
For different workpieces, various types of steel structure welding robot workstations are used to achieve modular assembly of steel structures. Between modular workstations, overhead cranes, intelligent sorting equipment, Automated Storage and Retrieval System (ASRS), and AGV unmanned transport vehicles can be fully utilized to construct a three-dimensional intelligent logistics and storage system within the workshop.
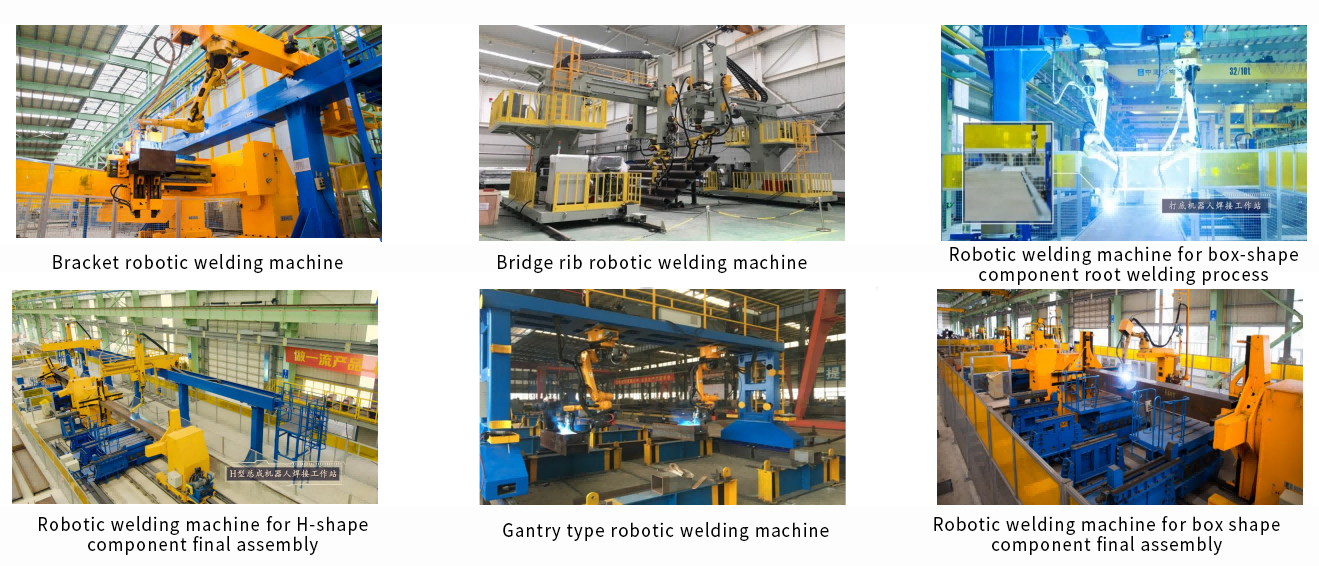
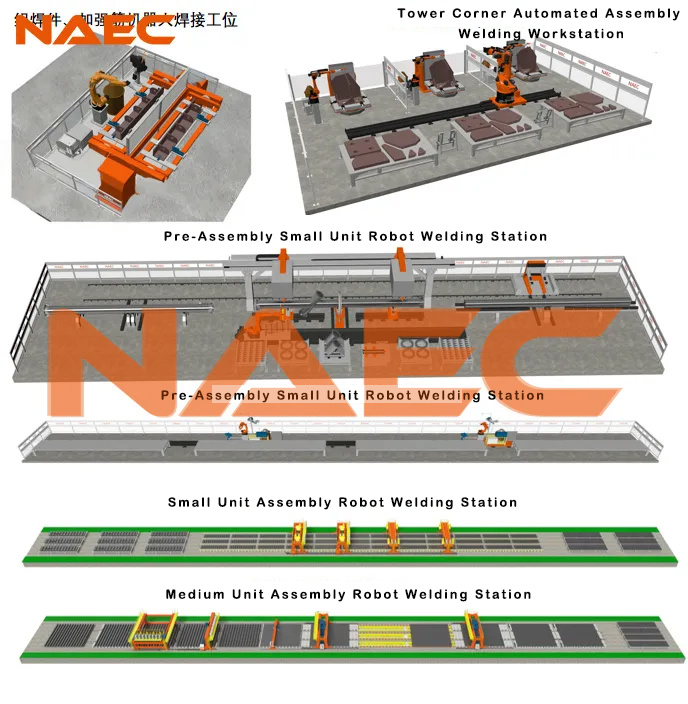
Lean Intelligent Manufacturing Solutions
Currently, for in-factory assembly and welding of architectural, bridge, H-shaped, box-shaped, and irregular steel structural components, as well as small group assemblies in shipbuilding—including splicing brackets, stiffening plates, and box partition welding—NAEC offers mature intelligent solutions.
With robots as the core, equipped with vision modules, structured light sensors are applied for high-precision, high-speed tracking and detection. This eliminates the cumbersome programming required for traditional teach-type robots and addresses the limitations of offline programming models, such as difficulty in meeting standards and narrow applicability. The solution is suitable for multi-batch, multi-type, and irregular medium-thick plate welding. Workpieces can be freely placed within the reach of the robotic arm, and processing capabilities can be expanded through positioners. The workstation features a fully graphical interface, allowing general operators to become proficient after 2-3 days of training. A single operator can manage 3 to 4 devices, significantly improving production efficiency. For the entire production line, data synchronization and information visualization are achieved, realizing true intelligent steel structure production.
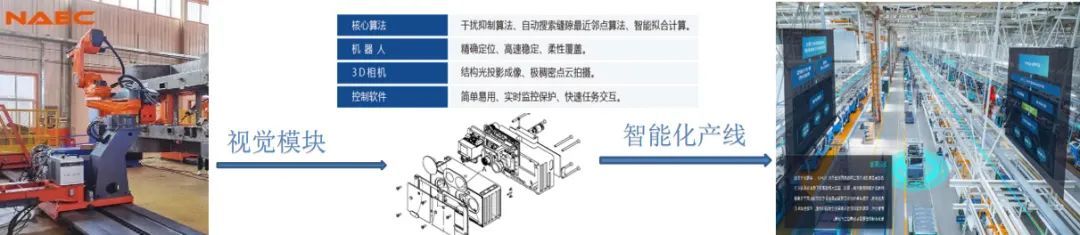
In addition, NAEC provides intelligent solutions for raw material preprocessing lines, steel plate cutting lines, intelligent coating, and intelligent warehousing, fully supporting the transformation of steel structure companies into intelligent production.
Project Cases
Submerged Arc Welding Robot
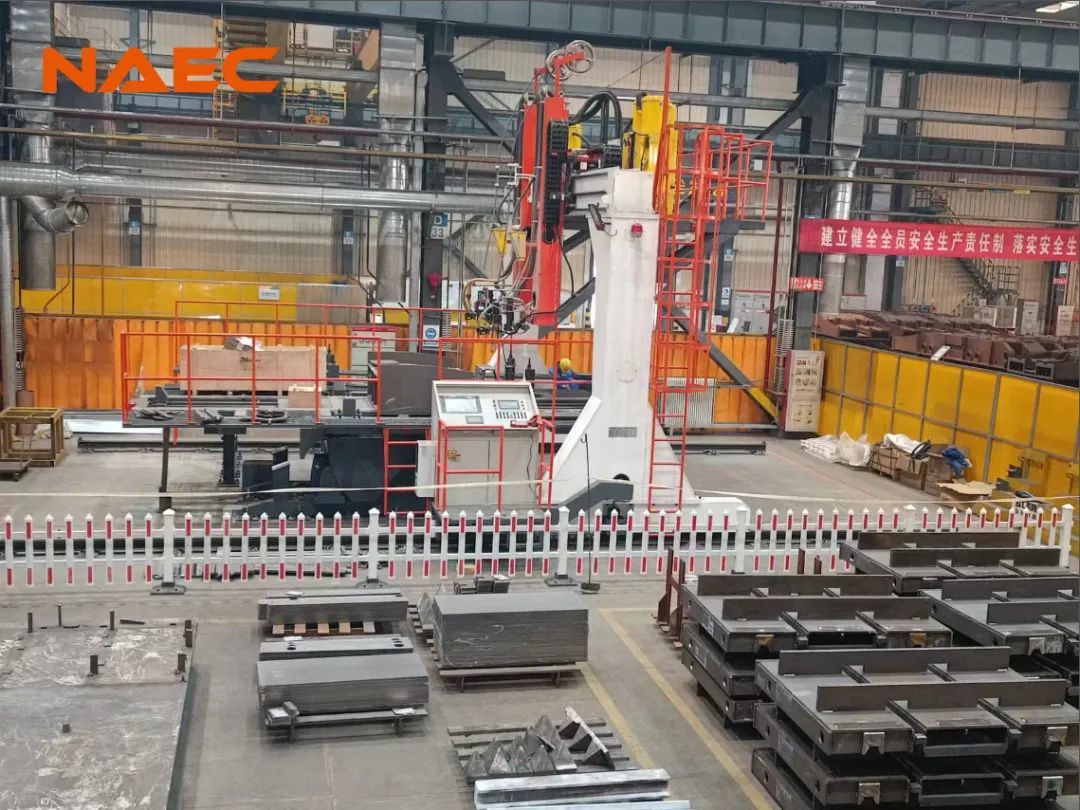
Gantry Boom Welding Robot
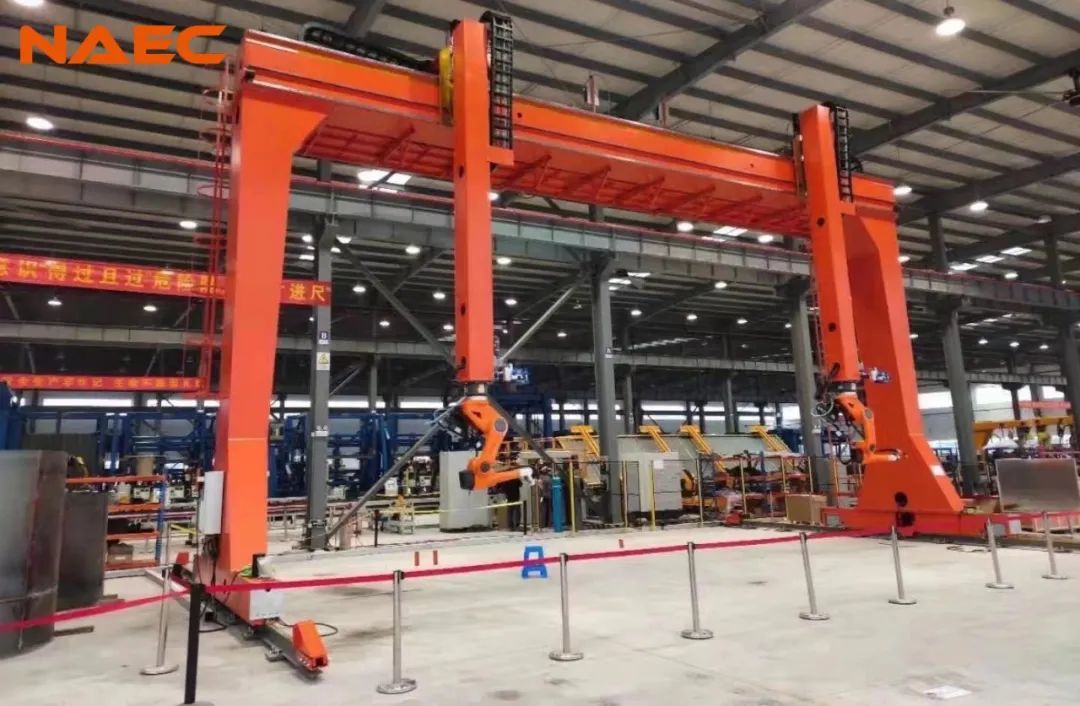
Positioners for Gantry Welding Robots
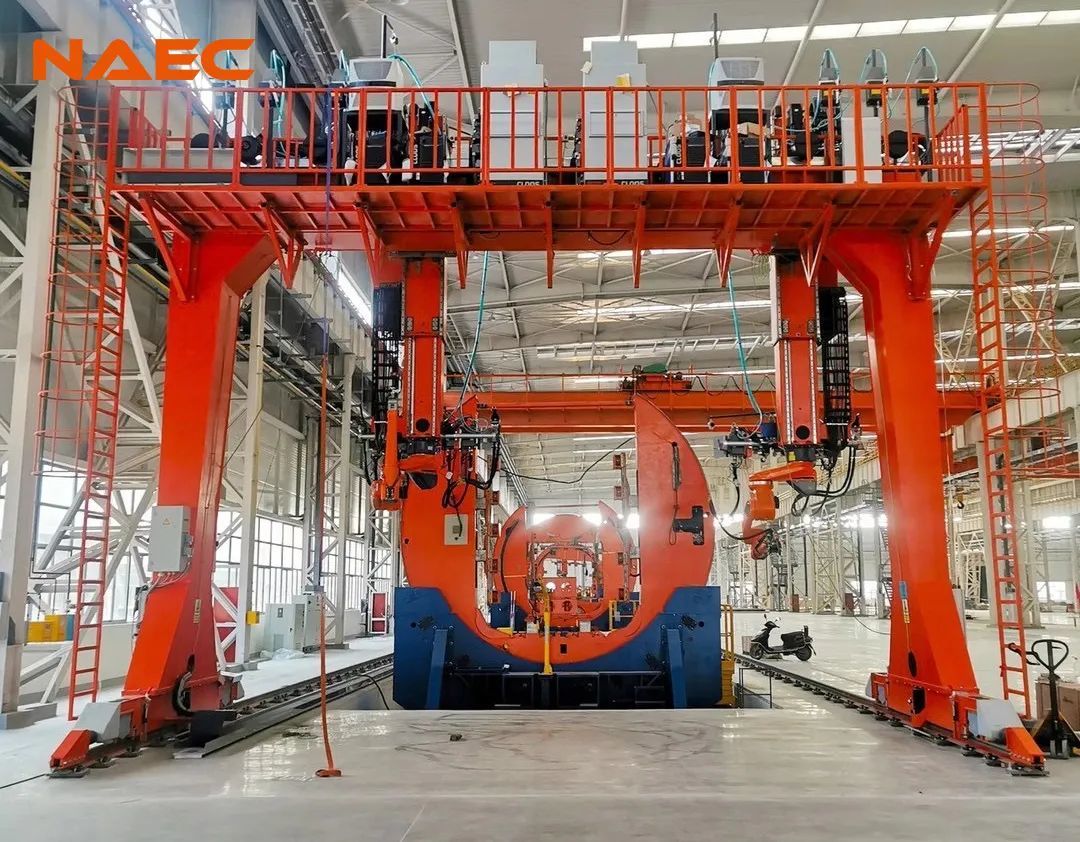
Related News
Email:auto@autowelds.com
Address: 11th floor, Building B4, Jiulong Lake International Enterprise Headquarters Park, No. 19 Suyuan Avenue, Jiangning District, Nanjing City, Jiangsu Province
aote
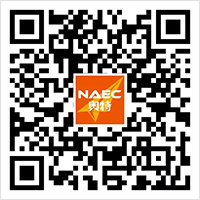
Auto Group Official Account
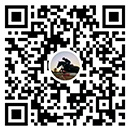
Auto Group Video Account
COOKIES
Our website uses cookies and similar technologies to personalize the advertising shown to you and to help you get the best experience on our website. For more information, see our Privacy & Cookie Policy
COOKIES
Our website uses cookies and similar technologies to personalize the advertising shown to you and to help you get the best experience on our website. For more information, see our Privacy & Cookie Policy
These cookies are necessary for basic functions such as payment. Standard cookies cannot be turned off and do not store any of your information.
These cookies collect information, such as how many people are using our site or which pages are popular, to help us improve the customer experience. Turning these cookies off will mean we can't collect information to improve your experience.
These cookies enable the website to provide enhanced functionality and personalization. They may be set by us or by third-party providers whose services we have added to our pages. If you do not allow these cookies, some or all of these services may not function properly.
These cookies help us understand what you are interested in so that we can show you relevant advertising on other websites. Turning these cookies off will mean we are unable to show you any personalized advertising.